Seattle Children’s uses Smartsheet to expand 3D printing for custom surgical care
With Smartsheet, Seattle Children’s can manage complex 3D printing requests and research data without requiring busy clinicians to invest time in learning new software.
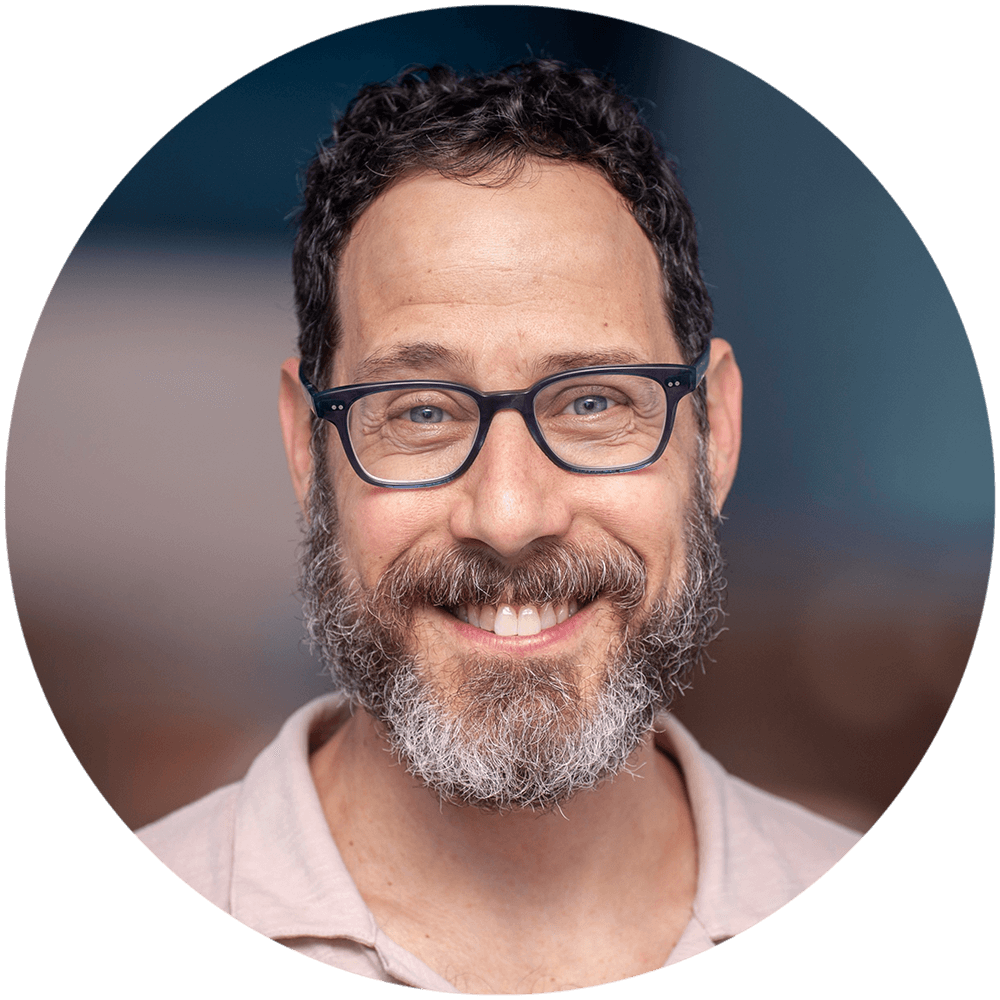
"Smartsheet allows me to do the work I’m supposed to be doing. I don’t want to spend my time learning a new database. I need to be talking to the surgeons: Was that model helpful, and how can we make it better? And Smartsheet just keeps running alongside that process".
Manager of Innovation Imaging and Simulation Modeling, Seattle Children’s
Seattle Children’s is designing the future of medical care. The hospital’s custom care program includes a 3D printing initiative that creates realistic anatomical models surgeons can use to visualize and plan complex procedures. The designs, the plan details, and the outcomes that surgeons report back are all managed in Smartsheet, building a framework for greater standardization and expanded capacity as the program evolves.
“Hospitals are saying we need innovation,” says Seth Friedman, Ph.D., manager of innovation imaging and simulation modeling at Seattle Children’s. “Everyone has been trying to figure out how we can house that innovation within our own walls. The pandemic certainly gave us examples of how that can be effective, and now we’re in a position to look ahead and think how we bridge this across other areas. We made a big investment in surgery because there’s the most potential value in the printer that we have now, which prints super-soft things that surgeons can use to make a difference in patient care.”
Friedman is part of the Center for Clinical and Translational Research, responsible for devising practical applications for clinical research. In addition to managing the 3D printing service within the Continuous Improvement and Innovation program, he oversees radiology research. Friedman needed a solution to track data and imaging files from multi-year research projects, printing requests, and discussions with surgeons and investigators. It also had to be flexible for other program needs and be easy to learn and use, with as few steps as possible.
“I oversee the radiology core that all imaging research flows through for the whole organization,” Friedman says. “We would get an email, and six months later we’d get another email with a bunch of attachments. And then someone would bring a file to our office. We had all this paper and these files that we had to control. The problem is that if a study starts and nothing happens for two years, you cannot remember anything about what you talked about at that time or what the protocol was. I realized that we could use Smartsheet as document control by putting tons of files in a single cell. It provided a spreadsheet, a card system, and a document repository.”
Before adopting Smartsheet, Friedman and his colleagues had tried a variety of platforms, from project management software to office tools to custom-built databases. The best worked well enough for about six months, until users found them too inflexible to accommodate new uses, and the search would begin all over again. Smartsheet ended that churn.
A foundation for a 3D printing “factory”
The surgeons at Seattle Children’s work with Friedman to develop 3D anatomical models that help them visualize and plan intricate surgeries, often on very small children. After discussing the details of the request — for example, a child’s airway to be prepared for insertion of a tracheostomy tube — and reviewing medical imaging, Friedman inputs project information into Smartsheet so he can track the request and translate the data into a design for the printed product.
Once the model is printed and cleaned, surgeons can work with it to more clearly visualize the part of the body on which they will operate. With the actual size and physical characteristics in front of them in 3D, surgeons can make more detailed plans than they could by relying on generic anatomical data, or 2D- and 3D-reconstructed medical images. They can also share the model with the patient’s family to help them understand the plan for their child’s care.
“A lot of what we’re doing with custom care is really intense, individual-patient-specific stuff,” Friedman says. “The metric I’m really concerned about is, did this change decision-making for the surgery? If I do 10 models and one of them changes that decision-making, that’s good. We have a dashboard system that we’re trying to optimize for collection and display of the data. And I’m hoping to use storytelling as well to figure out how we augment those metrics with what feels more important: What was the X factor of printing out a pelvis so the physician could say, ‘I see, this is what we need to do.’”
The current program is small; Friedman compares it to an artisanal cheese shop run by a single family. But as more requests come in, he sees using Smartsheet as the foundation for a more standardized program with clear process steps and predictable time frames for modeling and design, printing, and cleaning. Each print job will still be unique, like the patients they are based on, but it will be easier for colleagues to manage parts of the printing process and efficiently produce more anatomical models.
“A lot of project solutions and databases work really well in a linear system,” Friedman says. “But if your system is chaotic? I’m not that organized as a person, but I’m really good in chaos. If you need this tomorrow, I’ll get it done, there’s no question. But that’s a really bad system if you have other people that you need to bring in, so I’m hoping that Smartsheet will save me from myself. We’re using it to set up a system that is sustainable, that no one person is the linchpin for, and that has the flexibility to change over time.”
A data repository that fits everyone’s style
Friedman’s other major use of Smartsheet is for organizing imaging data and records for radiology research studies. Because weeks or months can pass between enrollments of new patients, the team needed a single place to capture study design and requirements that would be quick to review and follow even if it wasn’t fresh in their minds.
“The idiosyncratic quality of managing binders and documents can be really bad,” Friedman says. “We’ve been able to eliminate the issue where, if we have five different service lines and I send them all electronic documentation, one person will bind it in a spiral notebook; one person will throw it away; one will put it in a group email folder; one will put it in SharePoint. Now we publish a dashboard for each modality. The technologists know what research studies are present, and when they get a new patient, they can very quickly get the information they need to execute the process for a particular study.”
A platform that lets clinicians focus on what they do best
Whether they’re capturing research insights or reviewing surgical techniques, the staff at Seattle Children’s never lose sight of their mission to provide hope, care, and cures for every child. Friedman and his colleagues don’t always have time to learn new software skills or project management techniques, especially if it is outside their daily work. The ease of use and intuitive interface of Smartsheet allow them to focus on what’s most important.
Friedman is looking forward to using Smartsheet to expand and evolve the printing program. With dashboards to put program data at users’ fingertips, automation to reduce repetitive tasks, analytics to generate program insights, and easy cloud-based access, Smartsheet offers rich detail and flexibility to suit the level of personalization Seattle Children’s aims to deliver.
“Our current phase of work is a startup, ramping up to where we will ultimately be a year from now,” Friedman says. “We’ll have production at its maximum. We’re setting up the foundational tool to be able to run that factory and get metrics on cycle time, process, and impact. Once it is in full production mode, we can optimize so it becomes a learning system. If we were to spend six months to build a custom database and then say we’re done, that presumes the system doesn’t change very much, and I think the system will change a lot. It’s just the nature of healthcare.”
For more information about this story, please see our case study.